Environmental concerns are influencing a greater need for renewable and sustainable energy across the world with specialist technologies being at the forefront of new designs and solutions. As maritime industries begin to tackle the climate change issues, ports and shipping companies are looking for carbon-free alternatives by testing potential solutions for vessels. The requirement to make a move toward greener shipping is imminent. As companies start to concentrate their efforts in developing efficient solutions for improving performance and reducing emissions, engineers are applying their skills and expertise to support and contribute to the design of these advancements.
CFD (Computational Fluid Dynamics) technology has become a crucial support for naval architects, yacht designers and design engineers to optimise designs for critical elements such as weight saving, performance predictions, reducing emissions and design optimisation.
Cape Horn Engineering is a UK based company, best-in-class independent CFD consultancy with clients all over the world. They are industry leaders in CFD and marine technology solutions, specialising in performance prediction of cargo ships, renewable energy structures, racing sailing yachts, superyachts, motor boats and more.
Using specialist CFD technology
Cape Horn Engineering’s expertise is used to optimise the design of racing yachts, sailing yachts, power boats, superyachts, commercial ships and renewable energy structures, for clients all over the world. They have been at the core of simulation-based America’s Cup and Ocean Racing design campaigns for over 15 years, always pushing the boundaries. Similarly, they have vast experience in ship hydrodynamics, having been involved in yacht and ship design using CFD for the last 2 decades. They specialise in high-fidelity RANS-based simulation techniques where accurate forces and moments are obtained for the given shape candidates and operating conditions. For all simulations, Cape Horn Engineering use one of the best commercial software packages available, Star-ccm+ from Siemens PLM and have access to a large high performance computing cluster on the Cloud.
Their CFD methods cover a large variety of flow behaviours and includes free-surface flow, viscous flow, full-scale performance prediction, fluid-structure-interaction and dynamic behaviour. They can help win yacht races, improve performance, safety or passenger comfort, reduce emissions and save on fuel.
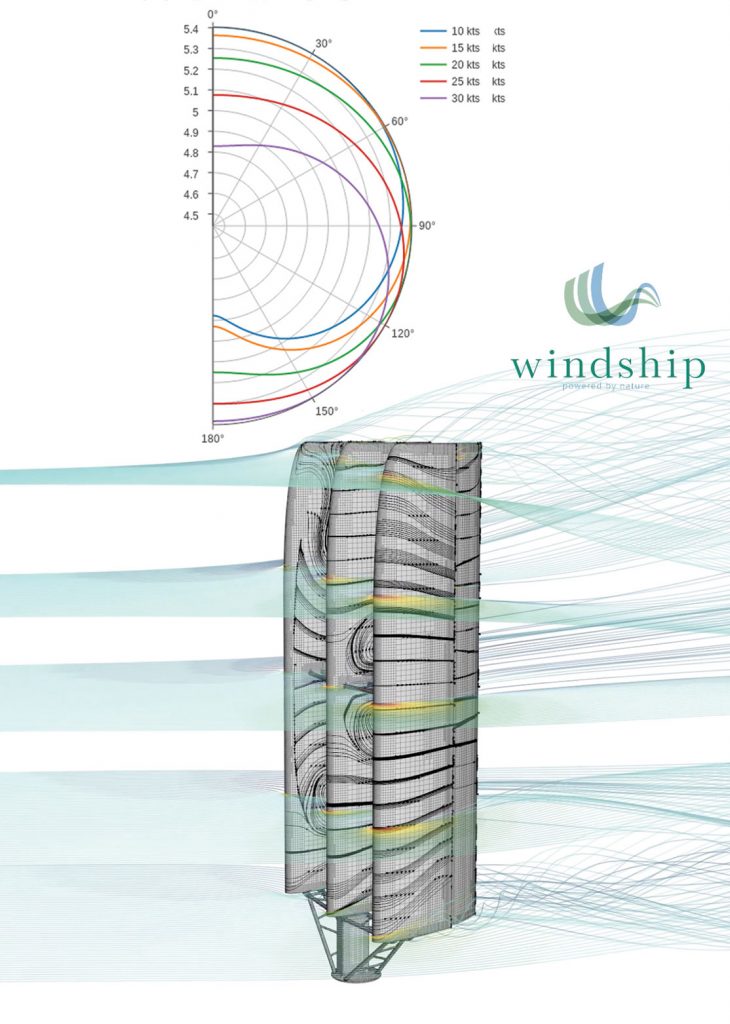
Wind Propulsion Technology (WPT)
To address the problem of global commercial shipping, the introduction of WPT (Wind Propulsion Technology) has been evaluated. According to some recent studies, wind-assisted ship propulsion using rigid wings, sails, kites, Magnus rotors or other novel devices on some specific vessel types such as bulk carriers and tankers, have the potential of fuel savings and emission reductions around 10 -30%. The IMO have recently acknowledged wind propulsion as one of the solutions for the shipping industry to meet decarbonisation targets.
Due to their renowned experience and specialist technology, Cape Horn Engineering are able to offer a holistic analysis of the benefits of WPT. They are supporting one of their clients, Windship Technology Ltd, a solid wing power concept that is being developed by a consortium of key players in the global shipping industry, which could revolutionise the way tomorrow’s vessels carry goods across the world’s oceans. The patented UK designed Windship rig system is consistently regarded as the most powerful fuel and emission saving wind system in the market, which will materially help the shipping industry move closer towards achieving its reduction in emissions.
Dr.-Ing Rodrigo Azcueta, Managing Director of Cape Horn Engineering, comments ”We are extremely proud to be part of the team led by Windship Technology for this exciting project, running a Computational Fluid Dynamic programme to further improve the design of the solid wings. One of the key focuses of our project is to provide a clearer, unbiased and more detailed analysis of the new technologies available. This allows interested parties to be confident in the investment of greener technology. The analytical evidence provided will give businesses a clearer understanding of the potential savings that can be realised with the implementation of the green propulsion systems. Without significant mitigating action it is projected that the global shipping industry could account for almost a fifth of carbon emissions by 2050.”
In order for the shipping industry to adopt these new technologies, the accurate analysis of the potential savings and the results must be presented to all stakeholders involved. In order to achieve this, improved simulation techniques are needed to optimise design and routing. Several factors need to be accounted for, including the aerodynamics of the thrust producing devices, the vessel hydrodynamics, propellers and engine types and the optimal routing.
CFD Simulations
Cape Horn Engineering were commissioned to run an extensive Computational Fluid Dynamic programme to further improve the design of the solid wings. A multitude of wing assembly shape configurations were analysed in varying wind conditions. In total, almost one thousand, high-fidelity CFD simulations were performed and analysed. The simulations were used to set up force models needed to describe the vessel’s hydrodynamic and aerodynamic behaviour. Operating conditions for the WPT devices are apparent wind angle and speed, wind shear and wind gradient (variation of wind speed and direction with height above the water surface), and angle of attack of the wings and its flaps.
A 2 digit percentage improvement in the aerodynamic performance of the wing assembly was obtained. Some selected simulation points were compared and validated with the wind tunnel testing, as well as with previous CFD analysis provided by Lloyds Register. Experts from the Wolfson Unit (University of Southampton) were also involved in the analysis of the CFD results. Extreme wind load cases were delivered to structural experts for assuring optimum weight and safety of the structures.
Further CFD design optimisation in 2020 will take the Windship concept ship into consideration as a whole, including the ship hydrodynamics, engine and propulsion, aerodynamics and optimal routing. The operating conditions for the vessel will be the advance speed and the drift, heel and rudder angles. Furthermore, windage on superstructures and the added resistance due to sea state will be modelled and taken into account.
Rodrigo Azcueta, managing director of Cape Horn, comments “When it comes to building a new ship, the design must be optimised to fit the wings on deck efficiently from both an operational and performance perspective. The design of hull features such as skegs or bilge keels might be required to balance the transversal instability induced by the installation of the WPT. Having a CFD model comprising of both the hydrodynamic and aerodynamic artefacts of the design will allow highly targeted design optimisations. Currently, wind propulsion systems and ship design are considered as two entities, hence they are designed independently. It is reasonable to believe that they should be designed as a whole from the earliest stage, due to the dependency of each aspect on the other. The optimisation process and predicted potential performance will determine the optimal operational points resulting in the lowest required engine power, fuel consumption and total emissions. The aim of our project is to facilitate the uptake of WPT’s. Moreover, we hope to enable the implementation of these technologies in the shortest timeframe possible”.